Recycling fee for drive batteries
Drive batteries: the recycling fee and what it is used for
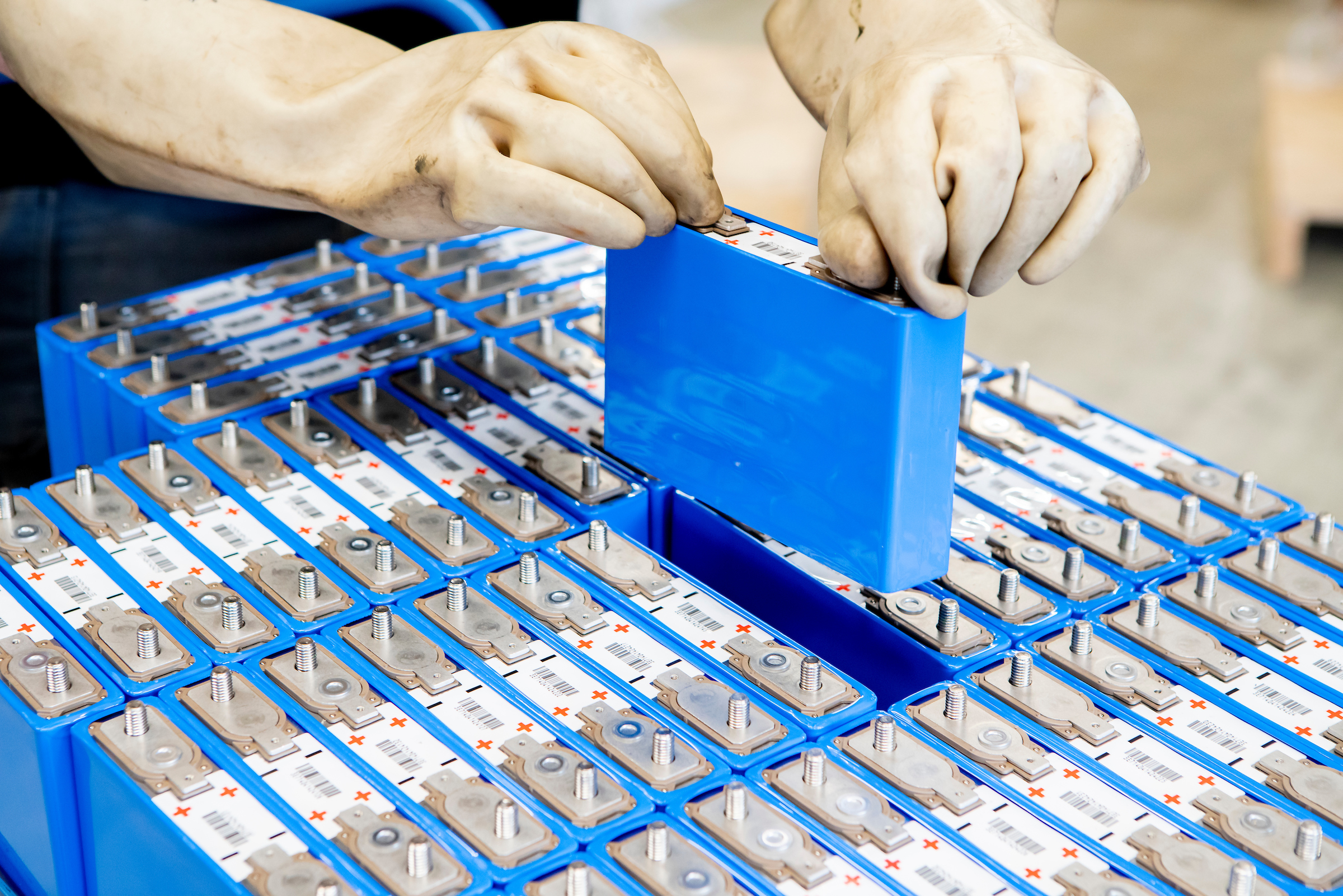
Manufacturers of electric and hybrid cars participating in the ARN Management Plan pay a recycling fee for drive batteries in cars registered in the Netherlands. The fee (in 2020 it was between €6 and €135) varies according to the weight of the battery and is collected by ARN. What does ARN use the money for?
According to battery-management legislation (Bbb), car manufacturers and importers are mandatorily obliged to take back end-of-life starter batteries and the drive batteries of hybrid and electric cars. Through their participation in a collective system (ARN Management Plan), manufacturers and importers can transfer the implementation of this responsibility to ARN. The bottom line for participation is the heavier the battery, the higher the fee. ARN uses the money for the collection and recycling of the batteries.
One collection company
As far as the collection of batteries is concerned, it must be stressed here that there is only one company in the Netherlands that is fully equipped to collect batteries from car and dismantling companies. That company is Van Peperzeel, in Lelystad. This accredited and specialised company collects the batteries at the request of ARN employees. Alongside Van Peperzeel’s relationship with ARN, the company also acts on behalf of Stibat (a Dutch anacronym for Battery Foundation) as a national sorting centre for all empty and end-of-life batteries in the Netherlands.
New lease of life?
Where the batteries are taken to depends on their type and condition. Here too, on the strength of agreed protocols, ARN is leading. Broadly speaking, it is a matter of whether the drive batteries are suitable to be processed for new applications, such as the stationary storage of energy generated by solar panels, for example. “Batteries that are in good condition and, more importantly, not damaged, might be suitable for second-life use,” says Hector Timmers, Quality Assurance employee at ARN. “If they are deemed to be not suitable, they are sent to battery processors in Germany and France, selected by us.”
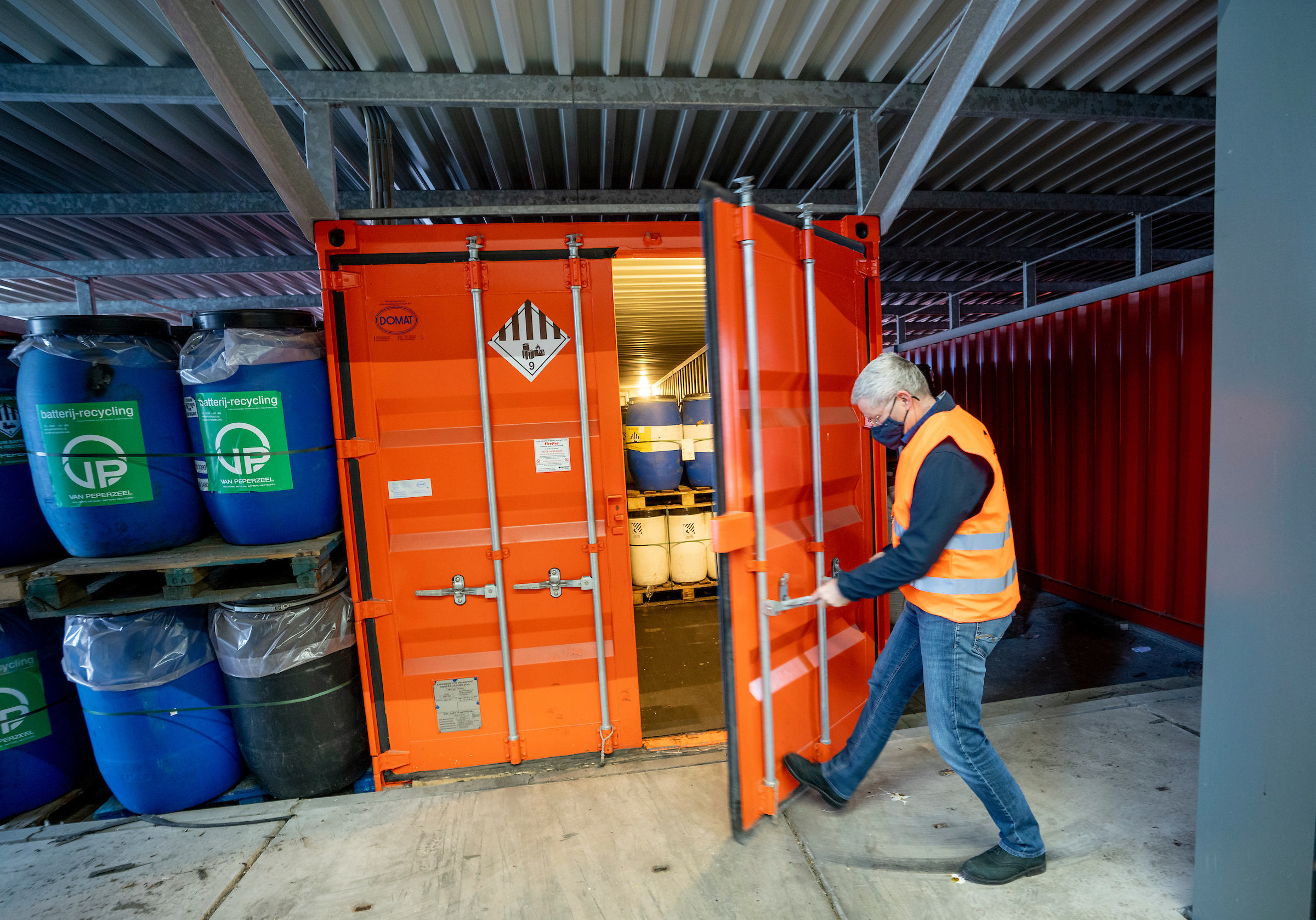
Used in a new application
The first of these two options – a second life – is an interesting proposition because what is being alluded to here is their actual reuse, not in a car, but in a completely different application. In the context of an end-of-waste framework, ARN is currently collaborating in this area with three other partners. An important legal consideration is that these partners formally assume the producer’s responsibility from the car manufacturer. They therefore assume responsibility for the battery to find a new, stationary application for it.
Batteries that are in good condition and, more importantly, not damaged, might be suitable for second-life use
Hector Timmers, ARN
Three partners
One of these companies, NPP Power Europe, gives end-of-life car batteries collected via ARN a second lease of life. This company, which is based in Ridderkerk, is active in the areas of solar panels for powering traffic signs, installations for the temporary storage of surplus energy, renewable installations and installations for back-up power.
Arnhem-based company Time Shift energy storage processes waste batteries to make them suitable for energy-storage systems, which are mainly used by energy companies. The third of these partners, EcarACCU, uses end-of-life drive batteries for the storage of solar energy. The reuse of drive batteries made possible by EcarACCU offer excellent solutions for supplying electrical power in remote areas.
According to Timmers, it is important for ARN to work together closely with these partners. “They give us a good idea of which batteries they can use and what condition they need to be in. The process starts up when a car or dismantling company indicates that batteries can be collected. Subsequently, based on the specifications of the manufacturers and second-use processors, ARN decides where the batteries will end up. If there is any doubt, we will consult, often with the aid of photos taken of the battery in question.”
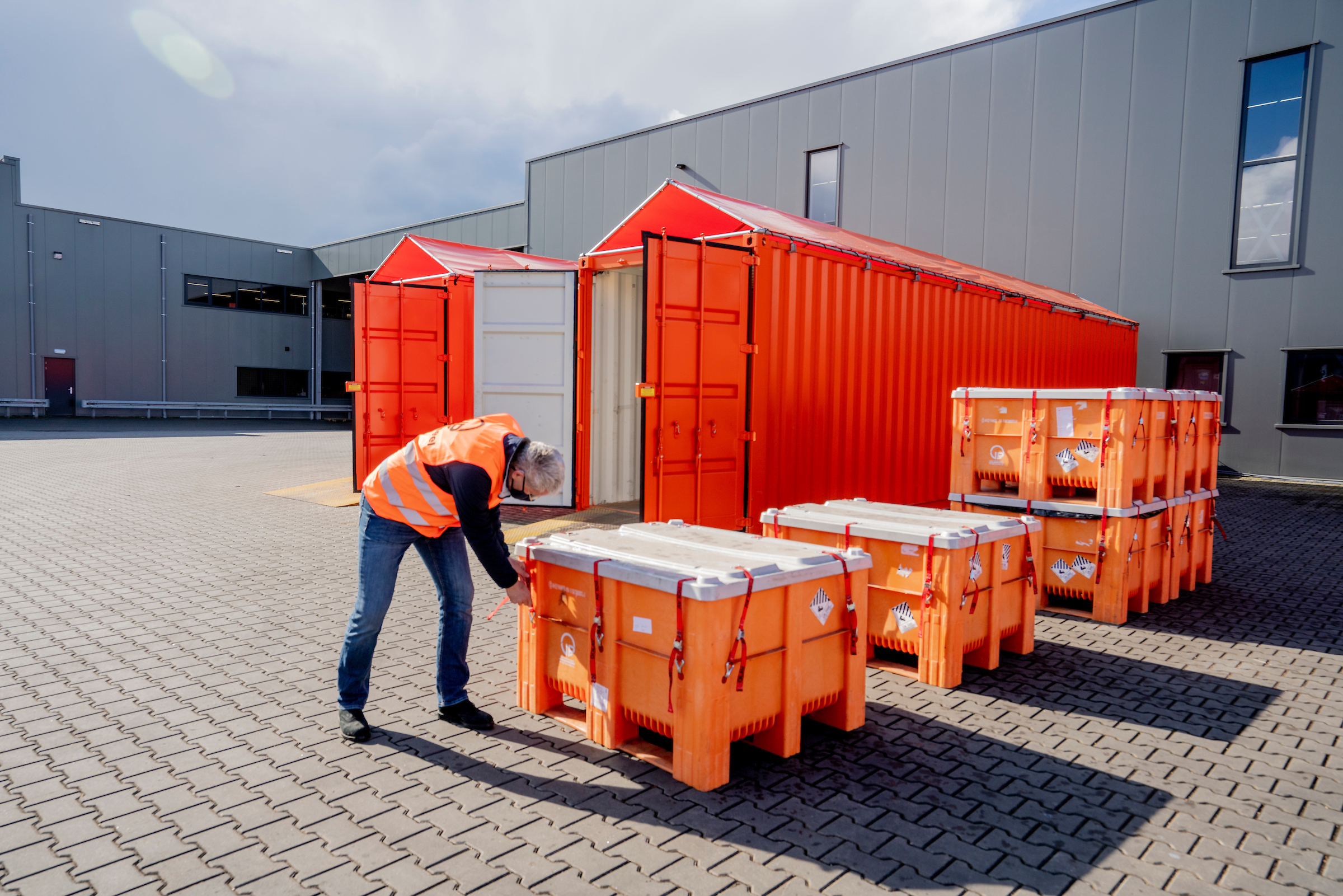
The process and the processing
At the end of the day, it is these three companies that decide whether they can use drive batteries for their respective applications, says Timmers. “If a battery cannot be given a second lease of life, there is always the alternative option of dismantling and processing. This is what usually happens to damaged batteries or modules – not complete battery sets.”
Several steps are involved in all this. Firstly, the battery is fully discharged, or neutralised in another way, to ensure it is completely drained. Only then is the battery safe enough to be dismantled. The wiring and housing are then stripped and the materials are separated. Depending on the processor, the modules/cells are further processed in a series of subsequent steps. Several techniques are involved in all this, such as pyrolysis, shredding, mechanical separation and hydrometallurgy.
Sustainable Development Goals
For the fourth year, ARN has measured itself against the benchmarks of the Sustainable Development Goals (SDGs) in the context of being “lean and green”. The SDGs depicted here apply specifically to the content of this page.
Recycled percentages
Thanks to the targeted use of the relevant techniques, the recycling efficiency is relatively high. The processing companies are able to recycle more than 70 per cent – by weight and excluding the casing – of a battery. And this percentage will almost certainly increase. In terms of reusing materials, experts expect that new techniques will make it possible to increase recycling efficiency to more than 90 per cent.
With the CO2 footprint in mind, it’s a pity that the batteries have to be transported outside the country for final processing. This is because there are, unfortunately, no final processors of batteries in the Netherlands. But in this context too, ARN operates meticulously. From time to time, ARN gets the processors of drive batteries to carry out an Ecotest, which provides insight into the recycling efficiency, as well as the CO₂ footprint of the process. The recycling efficiency is a factor that is included in reporting to the government.